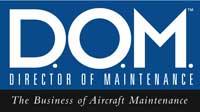
GLOBALPARTS.AERO ENTERS NEW ERA WITH UPDATED BRANDING, EXPANDED CAPABILITIES
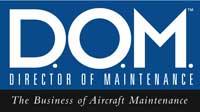
GlobalParts.aero, which maintained steady growth in it business and revenues throughout the recent economic recession, has announced major enhancements to its business. The Augusta, Kansas-based provider of aftermarket parts and services has added a new Federal Aviation Administration-certified repair station and in-house, build-to-print parts manufacturing capabilities to its operations. The company has also launched a new brand and expanded web presence.
“These moves allow us to broaden the support of our worldwide base of OEMS, business, charter and regional aircraft operators and provide them with a single, efficient and cost effective parts solution,” says
Malissa Nesmith, vice president and Chief Operating Officer of GlobalParts.aero. “This expansion also reflects the ongoing growth of our customer base beyond our original Raytheon and Hawker Beechcraft roots. We continue to value and service those clients, and we‘re pleased that we have also developed outstanding relationships with the industry’s full range of airframe manufacturers and their customers, as well.”
“The new repair station is fully-certified by the FAA and already in operation,” Ms. Nesmith notes. “It allows us to have complete control over cost drivers, turn times, and quality so that we can provide quick and competitive service to meet the needs of our customers. This will allow us to further expand our parts lists and control our inventories.”
Brad Vieux, Director of Business Development, also points to the addition of GlobalParts.aero’s new manufacturing capabilities and the company’s ability to accommodate larger and more extensive machining projects. “We have acquired factory-new machines to provide build-to-print manufacturing, including a Makino Mag 1, a 5-axis horizontal machining center specifically designed for high-productivity machining of complex parts for aerospace. “We can accommodate larger parts requirements — up to 60 inches — and work on hard metals such as steel and titanium as well as aluminum,” he explains.
Globalparts.aero’s new brand and website underscore the company’s operational and service expansions.
“When we incorporated in 2003, we went to the local office supply store and created our logo by cutting and pasting,” Ms. Nesmith recounts. “Originally, most of our customers just referred to us as ‘Global’ — the parts part was getting lost. Our name didn’t really reflect who we were or what we did. Now we’re emphasizing our core business and the industry in which we operate by combining the Global and Parts in the name and adding the .aero as part of our brand so that it’s not only obvious what market we serve, it provides the internet address, as well. We’re taking advantage of that by improving the graphics, information and access to our sales and support staff on website as well,” she concluded.
For more information visit www.globalparts.aero.