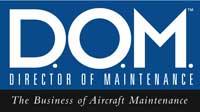
How to Prepare for the Big Maintenance Event - Engine Overhauls and Inspections
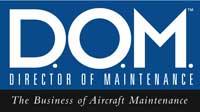
In part two of this three-part series, we discussed the steps you need to take to compare facility estimates and to help select a maintenance, repair and overhaul (MRO) facility for your major engine maintenance event. In this article, we will discuss what happens once your engine goes into the shop and how to monitor and control the event. There are many details to focus on to make this major shop visit successful, and if not addressed properly, they can add delays and unexpected costs.
We already selected the engine MRO facility to do the work. You should have the dates that the owner will allow the aircraft to be out of service for the event. The challenging part is coordinating everything between the owner and the MRO and airframe facilities. All three need to be on the same page or it can all fall apart. You must be prepared for countless changes during the event, so strong communication will be your best ally.
Many situations can cause delays and add expenses to the event once your aircraft has entered the shop. The owner may need to change the dates that the aircraft is available. The airframe or engine facility might not be able to accommodate this new date and keep the previously committed turnaround time (TAT). The coordination between the engine MRO and airframe facility might not be possible, so this can extend the down time of the aircraft and could cause a rippling effect.
The loaner engines or a maintenance team might not be available when you need them, so this could be another delay. Facilities can also have a shortage of manpower or delays with parts. The engine MRO facility can’t always make the committed TAT because of national or religious holidays, OEM part shortages, labor contract disputes (strikes), engineering approval delays from the OEM, and as we experienced recently, natural disasters such as with super storm Sandy.
This may sound ridiculous, but I have seen every one of these situations happen. These are all issues that you can’t control. The one thing you can control is clear communication. Some owners won’t accept any reasons for delays but you need to prepare the owner well in advance for any of these scenarios. It also helps to build in a time cushion of two or more weeks, depending on the work package. Have the discussion and explain to the owner that if he or she changes the aircraft availability dates at the last minute, it could get ugly.
In an effort to keep this major engine event on schedule and within the budget like we discussed in part one, the following paragraphs address the areas of concern when the engines are headed to the MRO facility.
Lease engines are commonly used so the aircraft can continue to fly during the event. Prior to receiving a lease engine, you will need to sign a bailment agreement and provide proof-of-hull insurance, listing the lessor as a beneficiary on the hull policy for the time the lease engine is installed on the aircraft. The lessor usually expects the underwriter policy to have up to $50 million in liability. You will need to list the lease engine serial number and the lessor in the insurance policy. A lease engine deposit might be required and is usually 50 to 100 percent of what the expected charges will be during the term. Keep in mind that you are responsible to maintain the engine while it’s in your control. Verify the airworthiness by reviewing the inspection status of the engine prior to installation.
Measurement of the turnaround time does not start until the engine reaches the shop floor, not the truck or loading dock. Remember, turn times have exclusions for delays not caused by the MRO facility. The facility will not be responsible if the engine does not arrive on time to the MRO facility, or there are OEM parts shortages, or if a special process outside the facility’s control causes a delay.
Prepayment might be required, based on the estimate provided. Arranging for payment could take time, so make plans in advance with the owner to avoid shop input delays. In most cases, the facility will not induct the engine without a deposit.
Shipping an engine requires insurance, whether it’s your engine or the lease engine. Don’t assume the facility or the lessor is covering it. Facilities aren’t responsible for getting that engine to or from the aircraft, so have a clear understanding of who is responsible and the type of coverage that is required. If you receive an engine that is damaged, don’t sign for it or accept it in that condition because you might have trouble filing a claim. I suggest uncrating or opening up the bag to at least verify there is no obvious exterior damage caused from a fork lift, etc.
Just before induction of the engine, you need to establish contact with the MRO customer manager for the event. Get a direct phone number, mobile number, email and contact information for that person and whoever is going to be the back-up contact for that customer manager. Communicate your expectations with the customer manager. I suggest you arrange for updates once a week or when a major item is discovered, such as foreign object damage (FOD) or replacing a costly part. Select your preferred source of communication such as email or phone and let the customer manager know that you want a condition report after teardown and inspection.
You will also need to issue a purchase order (PO) at the point of induction. The PO is your tool to control the cost of the event. The initial PO should only have the dollar amount sufficient to start the project and contain written instructions to the facility to only disassemble the engine and hold the wash process. This process is key in detecting any damage to the engine during the disassembly or if any FOD exists. If FOD is discovered, contact your hull insurance company immediately and don’t allow the engine to continue with the process until it is documented with pictures and measurements. You might need permission from the insurance company to continue with the process and it may require a visit from the insurance claims adjuster.
The next step is to revise the PO, giving the facility written authorization to wash and perform the inspection. Hold off authorizing repairs or the installation of new parts until a rejected parts list is produced. Plan on traveling to the facility to review all the rejected material but make every effort to avoid delays in the workflow — most shops run on a tight schedule. Perform a bench review by verifying the rejected materials list against the unserviceable (rejected) material. I usually request to have it all placed on a table in one spot.
Account for all material and part numbers on the list. With the exception of a few gaskets and retaining rings, you should be able to put your hand on every rejected part. If you come across an item that seems to have minor damage or is an expensive part, you can request to have it reinspected or have it evaluated for repair. If there is an item that can’t be repaired and you are not in agreement with the reason for rejection, it never hurts to have that item reinspected. Sometimes items can be on the thin edge of serviceable or unserviceable. Measuring tolerances of 0.001- to 0.005-inch can easily be misread by the way a gauge is held or the visual reference of an individual. Ask questions to better understand all the issues discovered and the type of rework available to correct these issues. Engines that enter for the first shop visit might be entitled to receive special pricing or commercial support from the OEM on certain items found as unserviceable. These items might be related to a commonly-known problem or to improve reliability. In order to receive this benefit, you will need to put in a request with the MRO or directly with the OEM to receive any special consideration for compensation.
This is the point where you need to know if there any parts shortages or back orders. You can also exercise options for replacing unserviceable material with exchange, repair or serviceable parts to control the cost or turn time of the engine. Remember, your negotiations prior to committing to that facility will allow you to exercise this option and help control the cost of the event.
The facility should provide a condition report that has the detail of all the major discrepancies found. These reports have pictures of the major findings and high-priced rejected items. The details in this report will help you explain to the owner all the costs of the defects that were found. Accompanying the report should be a revised cost estimate for the parts and rework required to return the engine back into service. Present this to the owner and make sure he or she is aware that this is not a final cost because there could be additional items that might fall out of tolerance after rework or during reassembly.
If you plan on using exchanged parts, there can be additional charges to bring your original exchange core up to the latest modification standard or if the core scraps out. Inquire if there will be additional time and material (T&M) charges and when those charges will be invoiced. These charges might not be invoiced until after the engine completes the shop visit.
Should you decide to install serviceable life-limited components in place of new, make sure there are sufficient cycles remaining to make it to the next event when you have access to that part. For the most accurate projection, base the cycles on the current flight profile. Be sure to measure the cycle-to-hour ratio from the past three to five years and not from the day the engine went into service.
The engine needs to continue with the rework and build process. Revise the PO to the facility by increasing the dollar amount to reflect what was provided on the revised cost estimate. There is still a chance for delays that can be caused by rework issues and parts availability, so monitor the progress and prepare for changes in the cost and estimated test cell date. Once the engine nears final assembly, you should be given a test cell date. If you plan on witnessing the test cell certification, make every effort to avoid delays or changing the date. Changing it can set you back several days. Although unlikely, engines can fail the test certification for many reasons including temperature margin, vibration and oil leaks. This could set you back two or more weeks, so be ready with your contingency plan and keep the owner aware of this possibility.
Depending on the payment terms, you should start preparing to make arrangements for the final payment to the MRO facility so the engine can be released in a timely manner. Request a preliminary invoice with all the parts details attached and allow time to review every part and labor charge on the preliminary invoice. With a large project like this, there can be glitches with the process and/or the computer programs used to track parts and produce an invoice. These glitches could cause double billing for parts. For example, there could be a part that was originally deemed scrapped after inspection and a new part was automatically issued in the system —but in the meantime, the original part was repaired and reinstalled into the engine. The new part remained on the list and was never removed from the system. Knowing the details of what was rejected and repaired will help you catch these items. If you find something, make note of it, complete your review and then contact the customer manager. Set up a time to review these items so the customer manager can correct them in the system. Don’t wait until the final invoice is issued.
After reviewing the test cell results, be sure to review the airworthiness release paperwork. Retain copies of any engineering orders for special repairs, technical variances and the traceability documentation for all the parts installed. Verify that all the component cards, service bulletins, advisory directives and service records have been updated correctly. Verify that the maintenance release is acceptable for your type of operation and is in accordance with your civil aviation regulations. Many people assume there will be an FAA 8130-3 form issued; sometimes you might only receive an FAA 337 form or Transport Canada release form TCCA-24-0078. It is important to ask the question and make sure you have an acceptable airworthiness release for your engine!
The engine work is now complete, the invoice has been paid and the engine is ready to ship. Obviously, the logistics and the timing all need to be coordinated to get the engines installed. It is sometimes necessary to have the MRO or OEM representative set up and rig the engine after installation to avoid any warranty or performance issues. Test fly the aircraft to assure the engines are closely matched. If there is a problem discovered, contact the customer manager immediately to have it corrected.
Many believe that MRO warranty policies should cover anything that could possibly fail or go wrong with an engine post-shop visit, but it can be more complex. The three warranty items you should focus on are labor, parts and performance. Ask for the actual warranty document before the event and understand the details. Warranties usually only cover workmanship and parts for the items that were changed or reworked. There may be many components that are sent to outside vendors with different warranty conditions.
I hope this article series has equipped you with a better understanding of this complicated maintenance process and has increased your level of respect for the preparation that is required for The Big Maintenance Event. Keep in mind that each facility has slightly different procedures. You might need to modify your approach based on the chosen facility. If you are interested in getting a copy of the entire three-part series, please email me at GKleros@JetSupport.com.
With more than 28 years of experience in aviation maintenance, management and field support services, Kleros is responsible for JSSI’s global technical operations. He currently serves on the Airworthiness and Maintenance Policy committee for General Aviation Manufacturers Association, is a board member of the Westchester Aircraft Maintenance Association, and is a member of the Professional Aviation Maintenance Association. He has served as the chairperson for the Trade Technology Board of the Stratford School of Aviation Maintenance.
Kleros holds A&P and IA ratings.