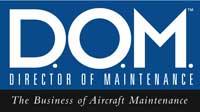
Quality and Safety
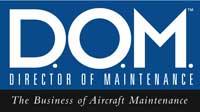
Why is “aircraft maintenance” a dirty phrase in an organization? Why does quality get such a bad rap? If you can consciously admit that those two questions are truthful, then it should come as no surprise that “quality aircraft maintenance” is an obscure and alien term.
Aviation businesses used to be run by those who were business savvy but passionate and knowledgeable about aviation first and foremost. They understood the integral nature of all the components of the business and how all those contribute to the aviation experience. They were cost conscious but also sensitive to needs of the business. Today, that appreciation is not as acute as aviation organizations are increasingly being run by people with financial versus aviation experience. Their primary concern is to maximize profits for shareholders. This is what is taught in MBA schools and is accomplished through increasing revenue and/or decreasing cost. Aircraft maintenance is a cost and quality is perceived the same, therefore they are not on the positive side of the balance sheet. A CEO of a major airline told me once, “We can’t get involved with that quality crap. We are barely keeping our head above water now.”
Even if your operation is a Part 145 repair station where aviation maintenance is the service you are providing, the formula remains the same: increased revenue + decreased costs = more profits. It’s all numbers. Business is run by numbers. As another CEO told me, “This is a business. What’s fair have to do with it?” That is the hard cold truth about the reality of business. It’s a cold-hearted numbers game.
Regulatory compliance carries weight because you could face a fine or business shut down if you don’t do as required. This cost gets attention, especially when things go wrong. It might come as a surprise, but following the FARs is not quality. The FARs provide the minimum threshold of performance (the bottom, not the best).
Safety also gets special attention and rightly so. Altruistically, we could say that the organization is concerned over the employee’s wellbeing by being safety conscious — but the reality is that it costs time and money when an employee is injured. Think dollars. The same is true with equipment damage; you can hang a pricetag on a damaged piece of equipment.
Let’s be realistic. Productivity makes the organizational financial wheel go ‘round. Anything that will get in its way needs to be dealt with, such as safety and regulations. However, you do what you can just so you don’t get caught. It’s the gamble that all organizations play and it keeps auditors busy. “Reuse that seal because it will take two days to get the right seal and this plane has to fly in four hours.” You know it’s wrong, but you inspect the seal. It looks perfectly good, so you reinstall it. Upon leak check, everything is fine and the plane makes its departure time. The supervisor is happy, the pilots are happy and the passengers are happy. Everyone is happy so where is the problem?
When things go wrong, how is it handled in your organization? What is the culture of your organization? This can be as subtle as an exchange between supervisors, “Don’t chastise my mechanic for standing on the top rung of a ladder. He has work to do and you’re hampering my production.” If you act and have the technician get the proper size ladder, you are the jerk for slowing someone else’s work productivity when nothing happens. If you do nothing and nothing happens, you are looked down upon as a meddler. If you do nothing and the employee gets hurt, you will be the guilty party for not acting upon the unsafe condition you witnessed. No matter what you do, you are going to be looked upon as a jerk, a meddler or an incompetent. Are your employees only compliant when they are being watched, or is it part of the culture? If so, then quality and safety have not been internalized.
Rules, regulations, policies and procedures are the controls reflecting the way things should be. Culture is how things really are and climate is how people feel about the whole thing reflecting the conscious. Only when the three are aligned do you have a safety- and quality-oriented high performance organization — otherwise all you have is lip service. What surprises me is when this duplicity is expressed in one sentence. “We never intentionally violate the FARs but those mechanics know the Boeing 737 and they don’t need B-check paper work to do that check.” Those words were actually expressed at a maintenance meeting by an upper-level manager. In that case the message is clear — get the job done and don’t violate any regulations, but production has priority.
Profit margins are slim in the MRO business. The big competitors are the Chinese who are working with the advantage of low labor cost. We are in big trouble if they ever get their quality act together. Not possible, you say? Depending on your age, all you have to do is look back about 50 years to the American auto industry. After WWII, there was a pent up demand for everything, and we bought whatever business produced. Primarily the American auto industry dictated what quality was and (beside some very expensive European cars) what we got we assumed was quality.
A few American quality gurus who were no longer needed for American business went to Japan to help rebuild their industrial structure. Initially, “made in Japan” was synonymous with junk but they had the advantage of cheap labor. Cheap junk is still junk. However, the American quality experts eventually had a tremendous effect in the Japanese industrial sector, especially the Japanese auto industry. They had such an effect that the Japanese auto industry almost wiped out the American auto industry. They competed on quality and as their wages increased to equal that of the American worker, they stayed competitive through emphasizing quality.
Are we in this situation now? Yes, we are, and it is coming from the Chinese. They are currently competing with us on low labor cost. In order to have an advantage, you don’t box a boxer or wrestle a wrestler — you do the unexpected. We need to compete in quality, not just cost. Improve quality and production cost decreases because of improved productivity and employee engagement. We can produce with less delay due to reduced quality issues and escapes. The customer is happier, management is happier and the employees are happier as well. As an extra bonus, safety issues decrease as quality increases. Realistically, all this happiness is not perpetual as this imperfect system requires constant vigilance from everyone. When things go out of whack, we need to recognize it for what it is — an opportunity for improvement.
You heard all the platitudes: “Do it right the first time,” “Quality and safety are everyone’s job,” and “Quality is job one.” They are all valid but in too many cases all they are only words. We try to instill quality and safety through intimidation, consequence and punishment. It needs to be grown in, not pushed in. Stay tuned for how a just culture is grown and how to get employee engaged in production.
Patrick Kinane joined the Air Force after high school and has worked in aviation since 1964. Kinane is a certified A&P with IA and holds an FAA license and commercial pilot certificate with instrument rating. He earned a bachelor of science degree in aviation maintenance management, MBA in quantitative methods, master of science degree in education and Ph.D. in organizational psychology. He has been involved with 121 carriers and held positions from aircraft mechanic to director of maintenance. Kinane currently works as senior quality systems auditor for AAR Corp. and adjunct professor for DeVry University instructing in organizational behavior, total quality management (TQM) and critical thinking. PlaneQA is his consulting company that specializes in quality and safety system audits and training. Speaking engagements are available with subjects in critical thinking, quality systems and organizational behavior. For more information, visit www.PlaneQA.com.