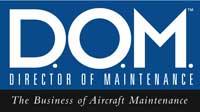
Steve King
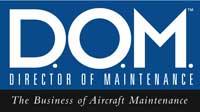
If your father is an aircraft mechanic, chances are high that you could end up working as an aircraft mechanic. Such is the case with Steve King, director of maintenance for Cox Enterprises. This month, D.O.M. magazine sat down with King to learn about his career journey to where he is today, some of the lessons he has learned along the way and some of the things he does to give back to the industry.
The Airline World
King grew up in Atlanta and his father worked for Delta Air Lines. “My father was the greatest influence on me,” King tells D.O.M. magazine. “He was a technician at Delta when I was very young. When I got old enough to understand what he was doing, he was an inspector. Somewhere between the age of eight and twelve, when dad was on midnight shift, he would sometimes take me to work with him. That’s what gave me the aviation bug. I was able to walk around
L-1011s, DC-10s and other aircraft Delta operated. I would hang around with dad as late as I could, and would ultimately end up asleep on the bench in the inspection office.”
Even though King was introduced to aviation at a young age, he went through high school not really knowing what he wanted to do when he graduated. When he found out that a friend was going to enroll in a local A&P school in the Atlanta area, he thought that would be a good idea for him to do. “My dad and I were always working on things,” King says. “It seems like we were always fixing something — whether it was a car, motorcycle or lawn mower. So I had a mechanical background. With the exposure I had to the airline world through my dad, it seemed that enrolling in A&P school would be a good move for me.”
King enrolled at Atlanta Area Technical College, a Part 147 school in the Atlanta area. After graduating from school with his A&P certificate, he thought the logical first step in his career was to land a job at an airline — but things don’t always go according to plan. “I applied with a couple of airlines, but the timing wasn’t good,” King shares. “That was shortly after Eastern Airlines went under. The airline industry was in a bit of turmoil. The market was flooded with former Eastern employees, and they ended up taking all of the open positions at the airlines. I had a couple of interviews, but they just didn’t pan out. So I decided to give general aviation a shot.”
King was working as a maintenance person repairing vending machines at Hartsfield-Jackson airport while he continued his search for a mechanic job. One day, he spotted a newspaper ad looking for an A&P mechanic at the airport. “The ad mentioned the need for an A&P mechanic, no experience required,” King says. “So I sent them a resume. They called me back, and it ended up being Cox Enterprises.”
In an ironic twist, the turmoil of the airline industry that prevented King from landing a job at an airline right out of school ended up giving him a chance to work at Cox Enterprises. “One of the things that had historically happened at Cox is that they would hire people with former airline experience,” King tells D.O.M. magazine. “But when the airlines were in re-hire mode, those people would leave. After a few cycles of that, the DOM at Cox decided maybe it would be a good idea to hire a young person out of school and train him, and maybe he would hang around. I’ve been here for 32 years. I guess it was a good plan.”
Cox Enterprises had a new GIII when King started working. Before landing the job, he says he didn’t even know what a Gulfstream was. But he quickly came to appreciate working in business aviation. “It was unique and interesting,” he shares. “I liked the fact that I wasn’t in the airline constant shift rotation that my dad was involved in. It seemed like every time dad got seniority and was promoted, he was at the bottom of the seniority list all over again.”
The Learning Curve
King was the only mechanic besides the DOM when he started working at Cox. Like most of us when we first started out working in aviation maintenance, the initial jobs to which he was assigned weren’t glorious. “The DOM had just hired a new kid out of school, so he wasn’t ready to give me anything responsible to do right away,” King shares. “So at first, I was primarily cleaning the airplane. I worked side-by-side him as we had inspections and maintenance to perform.”
King learned everything he could from the DOM, getting to perform maintenance tasks of greater responsibility as he went on. After two years, he went to his first GIII maintenance initial.
A year later, the company acquired a GIV, and he had the opportunity to learn a new aircraft. He continued to attend training schools and learn from his DOM through the years.
A Culture Shift
When Cox Enterprises acquired its second aircraft in 1997, a culture shift was taking place. The president of the company wanted to have a true transportation department. “We bought an airplane every year for five years, and we sold three aircraft during that time frame that we acquired through acquisitions,” King shares. “We also built a new facility during that five-year period.”
King became the DOM at Cox Enterprises in 1998, a year into that transition, when the former DOM retired. “When the DOM left, we had two airplanes,” King shares. “I was interviewing folks, and hired two people right away. We had another airplane on the way, bringing us up to three aircraft. And we were planning to add an aircraft every year. It was a busy time. It was like drinking water from a fire hose.”
The Transition to DOM
We asked King if there were any challenges transitioning from a mechanic to a DOM, especially in a rapidly-expanding flight department. “There were so many,” he laughs. “I think from an employee perspective, when I was a working DOM on the floor with two aircraft, the hardest part was ramping up to five aircraft. I had to understand that I needed to spend more time doing other things, not turning wrenches. My tools were now different. That was one of the toughest lessons.
“The other thing I learned from that transition is the importance of hiring great people,” he continues. “Hire the rock stars in the business, because they are going to make your life so much easier.”
Working in Business Aviation
King grew up around the airline world. Now that he has been working at Cox for 32 years, we asked him to share what it is he enjoys about working in business aviation. “Flexibility is key,” he says. “Corporate operations are much different than the airlines. When I first started out working here at Cox, I thought ‘I sure am glad I don’t have to do shift work like my dad does.’ But really, I went to work for the “Anytime Airline.” The flight schedule varies day by day. I didn’t really think about it at the time, but I have enjoyed it. It’s important to hire people that understand this is a 24/7 job. They need to know what they are stepping into.
“Another thing I enjoy about business aviation is the diversity of work,” he continues. “At the airlines, you might be in the engine shop, or you are the engine guy, or you are the hydraulics guy — that’s what I saw hanging around with dad. In corporate aviation, you need to be able to do everything. You need to understand avionics, engine and propulsion systems, bleed air systems — the list goes on. You work on the entire aircraft, and need to thoroughly understand all of the systems.”
Positive Work Culture
Another thing that King enjoys about working at Cox is the positive company culture. “Our company is very aviation oriented,” he shares. “Aviation is a great business tool for them and they recognize that. We are a part of the corporate culture, not just the hidden secret at the airport. The aviation department is involved in quarterly meetings. The leaders of our company stand up and say, ‘These people are key to what we do.’ It’s a great feeling to have that happen in a large corporate setting.
“An important thing that Cox does is pay for tuition,” he continues. “I push all my guys to take advantage of that. We have heard the horror stories in corporate aviation where all of a sudden the whole flight department goes away. I encourage my guys to take courses and get their degrees. I ask them, ‘How marketable are you today in the aviation community if everything goes away today?’ If you want to be a supervisor and grow in your career, you need to take advantage of advanced education. We currently have eight technicians. Four of them are in online college courses, and one is just starting his master’s degree program. All of our technicians are FlightSafety master technicians with the exception of one guy who has just been with us for two years. All of them are NCATT AET certified.”
Avionics is Key
King says that having a strong avionics understanding is crucial to being a successful A&P. He tells us that Atlanta Area Technical College now offers an additional course in avionics. Often as he is walking around in the school, students will ask him if it is worth spending the extra money to take the additional course. “You have to do it,” he stresses. “There’s no question about it. The technology in today’s aircraft is so advanced, if you don’t have that avionics knowledge you are handicapping yourself.”
King believes so strongly about having a strong avionics understanding that he requires all of his employees to be NCATT certified. “Our focus the last two years was to get all of our guys NCATT AET certified,” he says. “I’ve got to tell you, that has to be the hardest test I have ever taken. But it has really paid off.”
(For more information on NCATT and AET certification, visit www.NCATT.org.)
Being a Successful DOM
We asked King to tell us what he thinks it takes to be a successful DOM. “Keep the employees engaged,” he says. “Challenge them and have expectations. That happens by understanding your people. Give them all the tools you possibly can to help them be successful.”
Beyond technical training, another aspect King feels is important is professional development. “All of our guys have attended Global Jet Services’ Aviation Interpersonal Maintenance Management (AIMM) course,” he shares. “That’s another key to the total package for a maintenance person. Sure, it’s nice that you can turn a wrench. But as a corporate aviation mechanic, you are likely going to be standing with the principal of the company or high-ranking executives. That’s one of the things I am big on — I want to promote aircraft technicians as maintenance professionals!”
Mentoring Tomorrow’s Mechanics
There are many ways that King gives back to the industry that has given so much to him. He often spends time at Atlanta Area Technical College to mentor students enrolled in the A&P program. He also sits on the school’s advisory board and is the only corporate aviation person to have held that post. “I think A&P schools are challenged when it comes to understanding what is going on in our industry, especially in corporate aviation,” he tells D.O.M. magazine. “When I first sat on the board, I would walk into a class and talk to them about corporate aviation, and the kids didn’t understand what it meant to work in corporate aviation. Their instructors were former airline or former military guys for the most part. I have spent time educating the students and instructors about what we do in corporate aviation, and it has been well received.”
Another way King and his team mentor tomorrow’s mechanics is through their internship program. “My team mentors two aviation maintenance interns each year,” King tells D.O.M. magazine. “The Cox Aviation Internship Program was started in 2005 as a way to give back to the local business aviation industry. We accept applications in January and February from the local Part 147 schools (usually Atlanta Area Technical College and Aviation Institute of Maintenance[Lawrenceville campus]). While I may have started the program, our experienced A&P technicians are the real superstars. They willingly take the time to teach these new students all the details of aviation maintenance via shadowing. The interns are teamed with different technicians to allow for exposure to everything from tire changes, digital downloads and Nav database loading, to manpower and asset management.”
NBAA Maintenance Committee
Another way King gives back to the industry is by volunteering as a member of the NBAA Maintenance Committee. He joined the committee in 2007 and became the chairperson for the scholarship sub-committee in 2009. His objective is to grow the scholarship program and reach out to students and schools so they can understand what is about.
NBAA’s scholarship program is called Technical Rewards And Career Scholarships (TRACS). The program benefits people who are already working in the industry and students who want to come into the industry. “There are opportunities for current mechanics and students to apply for scholarships for OEM training courses from providers like FlightSafety, SimuFlite, Honeywell and others. When I came into the industry, one — I didn’t know anything about it, and two — if I would have had the opportunity to go out there and put a GIV maintenance initial on my resume, that would have made a huge difference. The industry is very competitive today. TRACS gives people the opportunity to either move up in their career or get their foot in the door to a corporate aviation job. Our objective through the TRACS program is to try to fill the talent pipeline in corporate aviation. If we can get people trained on OEM products, then service centers and OEMs are more likely to hire them.”
TRACS has given away 198 scholarships since it was introduced in 2007.
To learn more about TRACS scholarship opportunities, visit www.nbaa.com and click on the Professional Development tab.