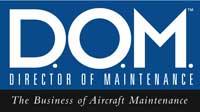
Wisconsin Aviation - Pete Schroeder, Vice President of Technical Services
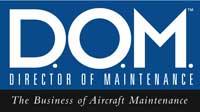
As he was spending time as a kid living on a farm in Southern Wisconsin, Pete Schroeder had no clue that he would end up working in aviation, much less be the vice president of technical services at Wisconsin Aviation. The lessons he learned on that farm, such as the value of hard work,learning to keep the farm equipment running despite limited resources and relying on and working with others to get the job done, have helped him be successful in his career. This month, D.O.M. magazine talks with Schroeder to learn about his journey from a young boy working on a farm to becoming a maintenance manager for a Southern Wisconsin-based FBO.
The aviation bug takes holdSchroeder wasn’t introduced to aviation by a friend or a family member. The only exposure he had to aviation was the annual EAA AirVenture in Oshkosh, WI, which he attended several times as a kid. He would always see the increased air traffic flying over the family farm as aircraft headed to and from the annual event.
His interest in aviation was sparked by a chance incident when he was in high school. “When I was a junior in high school, trying to figure what to do after graduation, our family was going on a family vacation,” Schroeder tells D.O.M. magazine. “As we were at the terminal in Milwaukee, waiting for our flight, I was watching the ground handler marshalling an airplane to the gate. As I stood there staring face-to-face with the captain, I thought, ‘I could do that.’ That’s how I started — I wanted to be a pilot.”
Pilot training
Schroeder enrolled at Gateway Technical College in Kenosha, WI. He obtained his commercial multi-instrument rating. His plan was to be a pilot, but his plans changed. “During my last semester at Gateway, I found out that if I wanted to be a pilot, I needed to build time,” Schroeder shares. “In order to build time, I would have to sit in a 152 and instruct. I didn’t want to build time that traditional way. I decided maybe I could get my A&P certificate and get a job in the corporate world as a mechanic.”
Off to Vegas
Schroeder says that he went to Las Vegas to visit his dad. He ended up staying there seven years. “A local vo-tech high school that had an aviation program had partnered with Clark County Community College to create a two-year A&P program,” he shares. “Nellis Air Force base had a big demand for their technicians to get A&P certificates. I enrolled in the two-year program at Clark County Community College and obtained my A&P.”
The first maintenance job
After graduating from A&P school, Schroeder moved from Las Vegas to Kansas City to be closer to his family. Once there, with both his pilot’s and A&P certificates in hand, he started looking for an aircraft maintenance job. He landed a job at the Kansas City Downtown Airport,working for Zantop International Airlines. He took a non-maintenance job to get his foot in the door while hoping an aircraft mechanic position would open up.
Schroeder got his first opportunity to work as a mechanic when he joined Baker’s Flying Service. Based at the Kansas City Downtown Airport, Baker’s was a full-service FBO. It offered flight training, rentals and charter.
D.O.M. magazine asked Schroeder if that first maintenance job was what he had expected. “It was better than what I expected,” he shares. “For the portion of my life that I grew up on the farm, I learned that you need to be resourceful in that environment. You need to fix stuff — you are hands on. That first aircraft maintenance job gave me the chance to be hands on, and I really enjoyed it.”
We asked Schroeder if at that point he had decided to give up his dream of being a pilot and instead pursue a career in aviation maintenance. “My thoughts were changing at that time,” he says. “I saw the life of a charter pilot. Before I got to work, they had already left for their charter flights. They got back after I had already left work. And when they got to their destination, they sat all day. I didn’t want to do that. I couldn’t be idle and just sit and wait. And I really enjoyed maintenance. It really worked for me.”
Wisconsin Aviation
Growing up in Wisconsin, Schroeder had been looking for an opportunity to move back to the area. He eventually decided to move back to Wisconsin in 1987 and start searching for an aviation maintenance job. “I came up here to Wisconsin and started to submit resumes,” Schroeder tells D.O.M. magazine.
Jeff Baum, president of Wisconsin Aviation, an FBO located in Watertown, WI, called Schroeder in for an interview. “Jeff was the first person I interviewed with,” Schroeder shares. “A couple of weeks later, Jeff gave me a call and offered me the job.”
Baum wanted to start a maintenance shop at his FBO. Schroeder was the first mechanic hired. He was the only mechanic for a while. He tells the story of Wisconsin Aviation’s first customer. “I got here the first day and Jeff told me he had an oil change for me to do. I said, ‘I can do that.’ We had oil. We had oil filters. So I brought the plane into the hangar and started to do the oil change. When I was ready to drain the oil, I realized — we didn’t have a bucket to drain it in! I learned to be resourceful from day one.”
As the sole mechanic, Schroeder wore many hats. You could say he was the mechanic, parts manager and floor sweeper, all wrapped in one. As business started to grow, more mechanics were hired. New hires were interviewed by Schroeder, Baum, and Chuck Swain, Baum’s business partner at the time.
Swain, who owned Beaver Aviation, a maintenance operation in nearby Juneau, WI, had partnered with Baum to start the maintenance operation at Wisconsin Aviation. Swain served as its first DOM. Russ Bargo, who was working as a mechanic at Wisconsin Aviation, took over as DOM in 1988. In 1990, Bargo moved on and Schroeder was promoted to DOM.
We asked Schroeder if there were any challenges transitioning from a mechanic to the director of maintenance at Wisconsin Aviation. “At the beginning, no, because we were a small group,” he says. “As a small group, everybody knew what the goals were and what the tasks were for the day. But as we grew and continued to add technicians, it became a challenge because it was harder to keep everyone informed on what the priorities were. That’s when I needed to become a manager — to manage the people.
“Becoming a better manager took time,” he continues. “Some of it was trial by fire. Jeff also supported me and helped me to grow. I also attended management courses and seminars when I could. It was a gradual growth. As the shop and the business continued to grow, my responsibilities continued to grow. I couldn’t have done it if I went from being a mechanic on the floor to the position that I have today. I would have failed. What allowed me to do it successfully was to grow with the company.”
Schroeder says another key to his growth has been The 20 Group. “We are a member of an organization called The 20 Group,” he shares. “It is a group of FBOs that share their information and help each other out. Originally, the CEOs would get together and meet once a year. Then they decided that it would be beneficial if the DOMs also got together and met. We now have a DOM meeting once a year with The 20 Group. It lasts three days. We go there with specific topics to discuss that end up evolving into many different discussions. The first year, I was hesitant to go. I didn’t know anybody and didn’t think I would get anything out of it. But when I got back, I thought, ‘Wow, that was great!’”
Apprenticeship program
Schroeder says that finding A&P mechanics to fill positions can sometimes be difficult in Wisconsin. One way Wisconsin Aviation has eased the difficulty is by having an apprenticeship program. It hires highly-motivated individuals who have basic mechanical aptitude, and has them work under the supervision of an A&P. “Right now, one of my best leads started that way,” Schroeder tells D.O.M. magazine. “He started out as an apprentice, got his A&P, got his IA and is now one of our best inspectors and one of our best leads.”
What are Schroeder’s tips for keeping the employees he has? “Help them grow,” he says. “Listen to everything they say and coach them along they way. Don’t belittle them or talk down to them. Give them new challenges. Reward them when you notice they do a good job. Offer constructive criticism when necessary.”
In the end, Schroeder is quick to tell us that he owes his success to the team at Wisconsin Aviation. “There is a lot of talent here,” he says. “Our success is because of everybody, from Jeff down to the newest technician. I have excellent managers that work for me, and they basically run the shops on a day-to-day basis. And they have great support personnel that work for them. They are the ones that really run this. I just challenge them to continue to find ways to improve our processes so that we can continue to grow.”