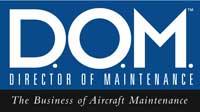
How to Prepare for the Big Maintenance Event: Engine Overhauls and Inspections
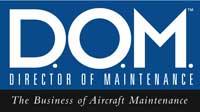
There are so many lessons learned from facilitating thousands of overhauls, like we have at JSSI over the years. I am asked frequently what the most important thing is when it comes to being prepared for a major inspection or engine overhaul. The answer is everything. There are so many important details that, if ignored, can send you down a road filled with delays and added costs. Most of these concerns can be avoided with thorough preparation.
Firstly, I suggest that you begin preparing for an event as early as possible. For light thrust engines, you should start to prepare about six to 12 months in advance. For an engine with more than 7,000 pounds thrust, you need to start as early as 20 months, but no later than 14, to avoid problems relating to the coordination of engine shop slots and rental engine availability.
Preparation for a big maintenance event starts with identifying everything that you need done before requesting an estimate. Notice that I mentioned estimate and not quote. The difference is that estimates are proposals for basic or average costs, not firm numbers. Quotes are usually firm prices, assuming all the possible costs are included. After the estimate phase in part two of this article, we will offer insight into understanding the estimate and the MRO facility selection process, and getting a hard quote that is not to be exceeded.
The first task is making sure you know what items on the aircraft or engine are truly due for this event. Believe it or not, engines and many accessories are sometimes overhauled or replaced when they still have several hundred hours of time remaining on them. This can come from errors in flight log entries that lead to errors in maintenance records and maintenance tracking programs.
Start by reviewing the maintenance tracking program (MTP). Verify part numbers and serial numbers by matching what is in the MTP against the logbooks and what is actually installed on the engine. Proper documentation that matches what is installed on the engine is essential to avoid unpleasant surprises. Often components are changed and their service cards or service records are not updated. You will need to provide traceability on each part for the shop visit. If a component and service card number do not match, you will be buying a new component. There may not be an option to exchange this part because the unit in question does not have traceability. Outright purchases are usually more expensive than exchanged parts. Bear this in mind to stay in budget.
Verify anything else that may need to be replaced based on cycles, not just hours. There are many items in the engine that are cycle driven. All the compressor and turbine rotors and some shafts have cycle life-limited components (LLCs). These cycle limits are considered hard time and can never be flown over the limit. It is highly unlikely to receive a waiver or ferry permit to extend operation unless there is a service bulletin (SB) issued by the original equipment manufacturer (OEM) that changes the limit. The calculation for some of these LLC components can vary depending on the engine manufacturer, model, type of operation or the location of that LLC within the engine.
Each OEM may count cycles differently and will list the cycle limits of each component and identify how the cycles are counted. The details can be found in manuals or service bulletins that provide cycle count factors and can be aircraft or engine serial number specific. For example, fan disc part number 100-2434 has a limit of 5,000 cycles and next to this number may be a reference like “(see note one).” Note one may contain a specific listed condition, e.g. “(except when installed in engine serial numbers WX123, WX124, WX125, and WX126).” These special conditions are usually associated with training aircraft where cycles are abbreviated and partially counted using special formulas.
Besides the hard time hourly and cycle limits, there are also soft times to consider. Some OEMs use a soft time limit as opposed to a hard time limit for certain items. Soft times are usually tracked by hours and sometimes cycles and allow the engine to operate past the published limit. This can apply to items installed in the engine or associated with the continued airworthiness inspection for on-condition engines. To explain this, let’s use turbine blades as an example. You can operate the turbine blades past their soft time limit, but they must be removed at the next shop entry or at the next time there is access to that area. The formula for tracking these limits may vary between engine models and within the different stages using different formulas.
Next, look at all the hard time and soft time items together throughout the engine. You may need to only access the engine for a hot section but discover there are some LLCs in the compressor section that will cycle out before the next time this area is due to be accessed for overhaul. It may be cost effective to have those items changed now, rather than cutting short the time between this inspection and the overhaul. As a responsible DOM, you also need to ask yourself the question of how this could affect the value of the aircraft if these items aren’t changed now. The owner could decide to put the aircraft up for sale just after the hot section, but if the full benefit of having a fresh hot section can’t be utilized, it will change the value of the aircraft. In my experience, the cost to perform the overhaul event early will usually get deducted from the asking price for the aircraft. Worst case scenario, it could deter purchase offers, so good communication with the owner now may help avoid an uncomfortable discussion later.
It is also important to consider what the aircraft’s mission/profile going forward will be before an overhaul. I have been involved in many situations where an aircraft had been operating 2.0 hours for every cycle but the operation then changed to 0.75 hours per cycle. This occurs sometimes with a new owner or change in the aircraft destinations. If a plane is stored at a separate location and has to reposition to pick up passengers each time without any long flight legs to offset a quick jump, the hour-to-cycle ratio decreases and changes inspection and repair requirements.
Next, review anything else that might be due for inspection on the airframe pylon. There are some items located in the pylon or thrust reversers that you will have easy access to, once they are off the aircraft and exposed. Research the items due in these areas to save future down time and expenses.
Make sure to research service bulletins/advisory directives (SB/ADs) that affect your model and educate yourself on the details and the required compliance. This will be essential when you solicit estimates for the work. Keep in mind that some SBs may be recommended by the OEM but not required for the engine to receive a hot section or overhaul sign off from the MRO facility. Many MRO facilities include ADs and mandatory and recommended SBs in their estimates. Watch out for how these are categorized or identified in the estimate. We will cover this fully in part two, but it is always good to familiarize yourself with all the SBs on your engine. OEM forums are good sources for the most current information on SBs and issues on the engine are. The OEMs typically provide thorough updates at maintenance and operations (M&O) sessions held throughout the year and often during industry events. If you can’t attend, ask for a copy of the latest M&O session from the OEM representative.
After hours of preparation and research, you know what the work scope for the event involves. Next you need to make at least two copies of all the log books and include the LLC cards, line replaceable units (LRU) cards, the service records and the service bulletin compliance section.
Keep the originals in a safe place and avoid sending them whenever possible. Scanning pages out of the log and emailing them is a great way to request estimates. The only time the log books should leave your possession is when the engine is heading into the shop. They should always remain with the engines firmly attached or, if necessary, shipped by first-level-priority courier with tracking options and in a waterproof and secure package.
You are now ready to solicit estimates, so it’s time to narrow down which facilities you want to consider.
Research the facilities that are authorized to perform heavy or major work on your engine model or airframe model. Keep in mind that there are few one-stop shops that can handle both major engine work and heavy airframe work. Some facilities subcontract the actual engine change and engine hot section or overhaul work, even though they claim to have full capabilities. Some of the OEM-owned shops and OEM-approved shops do this, and I’m not saying there are problems when this situation exists — it’s just a few more variables added to the equation to keep in mind. Just because the large MRO-authorized repair facility accepts the work and sub-contracts out some of the work, it does not mean they will automatically accept liability for potential mistakes by the subcontractors. Know who is working on your aircraft and understand their capabilities and limitations. I urge you strongly not to overlook this detail.
It is important to take the time to go online and gather information about the facilities. Look for information on blogs, Web sites, etc., and ask about places that work on your model. You will be surprised at the amount of feedback you can get and how quickly you can get it. I highly recommend consulting with an operator that has the same engine model as yours and that has been through a recent event. Word-of-mouth endorsements are valuable and prior real-life experiences, good or bad, will help you decide where to go and what to expect. One thing to remember is that blogs can be helpful but are sometimes used to vent frustration and even exaggerate an experience. Don’t let the blog be your sole source for making a decision. Trust your gut and plan on getting multiple estimates.
Reach out to the facilities you have selected for estimates and mail or scan and email your log book copies. Most of the MRO facilities have sales engineers that will visit your facility, review the engine documents you provide to them and present you with a proposal. It usually takes one to two weeks to get a proposal, so plan ahead.
There is much more to consider once you get all the estimates back and before making a final decision on which facility to use. We will continue this discussion and offer more insight on “How to prepare for the Big Maintenance Event — Part Two” in an upcoming issue of D.O.M.
George Kleros is responsible for JSSI’s global technical operations and has more than 28 years of experience in aviation maintenance, management and field support services. He currently serves on GAMA’s airworthiness and maintenance policy committee, is a board member of the Westchester Aircraft Maintenance Association since 2009, and is a PAMA member. He has served as the chairperson for the Trade Technology Board of the Stratford School of Aviation Maintenance. He holds IA and A&P FAA ratings.